In ancient Egyptian art no representations have been found of the sawing of stone by means of a copper blade and an abrasive (Lucas & Harris 1962, Stocks 1999), nor has any lapidary slabbing saw been found in the archaeological record (Arnold 1991). However, the ancient Egyptians had copper saw blades, which they employed in carpentry, and are frequently represented in Egyptian art (Fig. 1a). Examples of carpentry saws from very early in the ancient Egyptian civilization (1st-3rd Dynasty) have been found (Emery 1972, Arnold 1991). These early copper saws are of a variety of lengths up to 40 cm (image). Usually, only one edge of the blade is serrated and meant to be pulled and not pushed during cutting (i.e. rip-saw), and the blade is socketed into a straight wooden handle (Fig. 1b). An example of a fragment of an ancient Egyptian copper saw can be found at the Petrie Museum (UC30854).
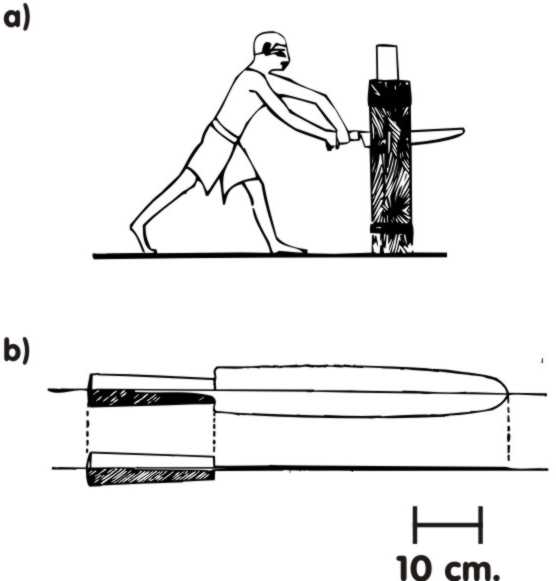
b) A 1st Dynasty copper saw (after Emery 1972).
The use of saws as a method of cutting rock is inferred from marks observed on ancient Egyptian stonework, including pieces of waste rock and finished and unfinished stone objects. Many of these marks have been found, usually observed as grooves cut into surfaces of rock or as striations on cut surfaces (Petrie 1974, Lucas and Harris 1962, Arnold 1991, Stocks 1999; 2001). For examples:
a) Saw marks on greywacke “schist” leaf-shaped bowl (1st Dynasty, Emery 1972 (pl. 39a)).
b) Chevron-shaped sawing marks on Sekhemkhet’s travertine (alabaster) sarcophagus (3rd Dynasty, Goneim 1956).
c) Saw marks on the lid of the granite sarcophagus of Meresankh (3rd Dynasty, Lucas and Harris 1962).
d) Saw marks on the granite portcullises of the Great Pyramid (4th Dynasty, Petrie 1974).
e) Saw marks on the granite sarcophagi of Khufu and Khafre (4th Dynasty, Petrie 1883).
Drawing #1 shows a saw cut on end of Khufu’s granite sarcophagus (Fig. 2) in the Great Pyramid.
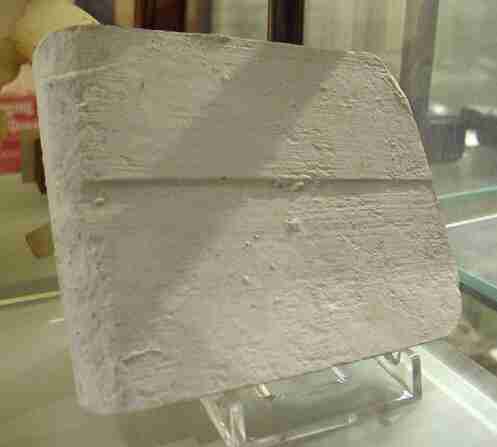
f) Saw marks on the basalt paving stone near the east side of the Great Pyramid of 4th Dynasty date (Fig. 3, Petrie 1883, Image).
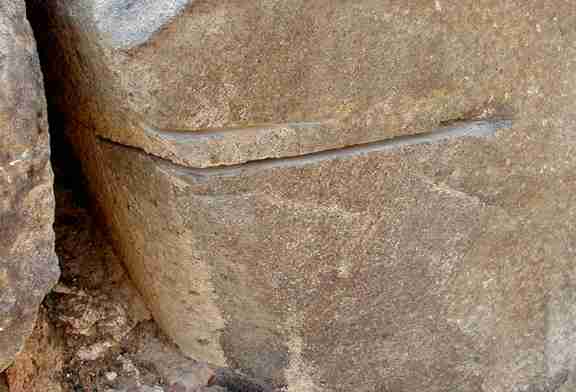
g) Saw marks on the granite sarcophagus of Hordjedef (4th Dynasty, Reisner 1931).
h) Saw marks on the back of one of the greywacke triads of Menkaure (4th Dynasty, Lucas and Harris 1962, Clark & Engelbach 1930 (pl. 247)).
i) Saw marks on two unfinished travertine statues of Menkaure (4th Dynasty, Reisner 1931).
j) Joint faces of casing blocks of Shepseskaf’s Mastabat el-Fara’un (4th Dynasty, Arnold 1991).
k) Saw marks on the travertine alters in the sun temple of Niuserra (5th Dynasty, Borchardt 1905).
l) Saw marks on basalt paving blocks in the mortuary temples at Niuserra (5th Dynasty, Borchardt 1905).
m) Saw marks on limestone blocks from the pyramid complex of Niuserra (5th Dynasty, Borchardt 1907).
n) Joint faces of casing blocks on the pyramid of Unas (5th Dynasty, Arnold 1991).
o) V-shaped slots in Djedefre’s rose granite sarcophagus (9th Dynasty, Stocks 2001).
p) Joint faces of casing blocks on the pyramid of Senwosret I (12th Dynasty, Arnold 1991).
q) Petrie (1883) gives additional examples of saw marks. Drawing #2 Fragment of hornblende diorite/granodiorite (‘syenite’) found at Memphis (UC16032) showing cuts on four faces. Petrie (1883) suggests this probably was made from removal of waste rock during the carving of a statue. Drawing #4 Basalt fragment (Petrie Museum Catalogue UC16034) showing saw cut of 4th Dynasty date. Drawing #6 Slab of diorite bearing equidistant parallel grooves of circular arcs which have been nearly polished out by crossed grinding. Petrie (1883) suggests the only feasible explanation of this piece is that it was produced by a circular saw.
r) Basalt fragment ( (Petrie Museum Catalogue UC16035) sawn nearly in half from both sides, of 4th Dynasty date.
s) A small unfinished statuette of quartz crystal (Petrie Museum Catalogue UC16617) demonstrates the removal of waste rock and the rough shaping of the front and sides by the use of a small lapidary saw (Petrie 1974).
t) A cube-shaped fragment of limestone (Petrie Museum Catalogue UC16043), sawn on 5 faces from the 4th Dynasty.
u) Colossal sandstone paw (Petrie Museum Catalogue UC29190) from a couchant figure of jackal, with saw marks on base where it was sliced for re-use, 18th Dynasty.
v) A fragment of quartz or basalt (Petrie Museum Catalogue UC16040) exhibiting numerous, parallel saw cuts of unknown date.
Early ancient Egyptian lapidary slabbing saws would have been made of copper, either cast or cold-worked until the Middle Kingdom, when bronze tools became more available. At this point in their history either copper or bronze would likely have been used until iron began to appear in quantity during the New Kingdom period (late 18th Dynasty), which gradually increased in availability until it became as common as bronze in the 26 Dynasty (Arnold 1991). Petrie (1883) has suggested that the rectangular bronze or copper slabbing saws were up to 2.7 m in length and about 0.75 to 5 mm in thickness. These were used for the cutting of a variety of rock objects, including granite sarcophagi. Laurer (1962) suggested that a thin copper sheet in the form of a hand saw was used to make the front edge of closely jointed, limestone casing blocks as early as the 3rd Dynasty. Stocks (1988) demonstrated that a flat-edged copper saw blades 5 mm in thickness could be made by poring molten copper into a shallow open mold. Copper, bronze, and iron are insufficiently in terms of indentation hardness to cut by abrasion hard stones such as basalt, diorite, granite, greywacke (schist), and siliceous sandstone (quartzite). A harder material than the metal itself is required as an abrasive in order to cut these rocks. This abrasive material could have been used either as shards of mineral aggregates or crystals used as cutting teeth, charged copper or bronze (small abrasive grains impregnated into the metal), or as a loose abrasive.
A jeweled cutting surface was suggested by Petrie (1883) for the cutting of hard stones (i.e. those rocks that contain mainly minerals with hardnesses greater than 7 on Mohs’ scale (Mh.)), in which jewels, such as beryl, topaz, chrysoberyl, corundum, or diamond, were needed since they are all harder than quartz (Mh. 7). As pointed out by Lucas and Harris (1962) Petrie omitted quartz, which will also cut quartz. Quartz will cut quartz or any mineral less hard when used as an abrasive, either as loose abrasive grains (Stocks 1993; 2001), or as quartz crystals or flint shards attached to the blade. A simple experiment was conducted to test that quartz can be used to cut quartz in this manner. A wedge-shaped shard of quartz was attached to the end of a wooden toothpick with coarse thread and cyanoacrylate glue (Fig. 4). The tool was sheared across a piece of quartz (amethyst) for about 1 hour with very little pressure, during this time the quartz shard was replaced as a result of wear due to abrasion. A horizontal groove was produced, and is about 1 mm in width with a depth of about 0.3 to 0.5 mm (Fig. 5). The surface of the groove is smooth and polished and has a rounded shape. The test demonstrates that a shard of quartz will abrade quartz using very little pressure. It would be expected that the rate of rock removal would increase as pressure was increased on the tool.
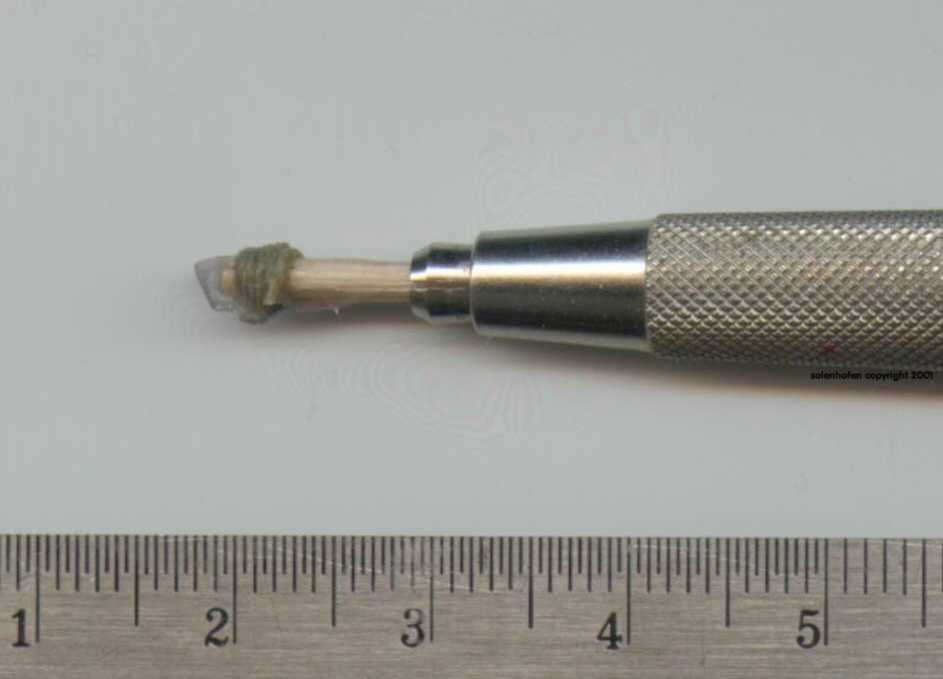
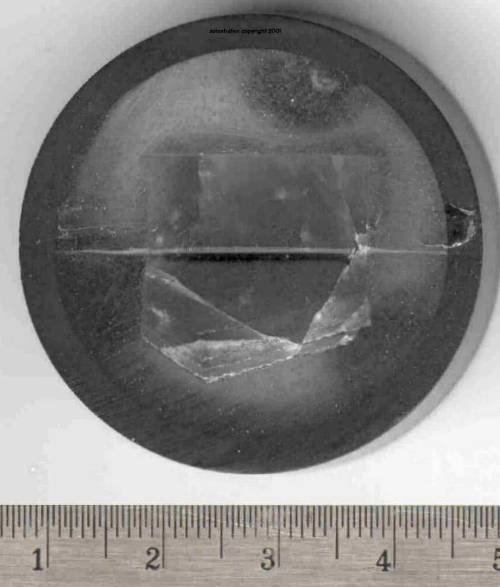
However, the problem with the use of quartz as cutting teeth is that the quartz teeth will also abrade as the rock is cut, if the material being cut is of equal hardness, rounding off the sharp edges and reducing their effectiveness as an abrasive. When used for rocks that contain quartz, the teeth would need to be of minerals that were harder than quartz in order to be an effective method of cutting rock, as originally pointed out by Petrie (1883). However, the brittle nature of many of these harder minerals still means that over time the sharp edges will wear off due to the stresses imposed on the cutting surface of the teeth during abrasion, again reducing their effectiveness as an abrasive. Zuber (1956) rules out the used of flint shards embedded into a metal frame as a method of sawing rocks by the ancient Egyptians. It is unlikely that the ancient Egyptians had a ready source of mineral abrasives with hardnesses greater than that of quartz (Lucas and Harris 1962). The most likely abrasive is loose quartz sand, with its ease in replacing worn abrasive grains, as the material used for cutting rocks for most of the ancient Egyptian’s history. An example of a 4th Dynasty basalt fragment can be found at The Petrie Museum, in which the saw cut still contains rock tailings and sand (UC16033).
Hand powered slabbing saws used for cutting rock were also known in other ancient civilizations. The Chinese used bow-saws with coiled bronze wire blades (Fig. 6a) for working jade (Long 1976), along with other tools, such as the partial rotary mud-saw (Fig. 6b). These types of lapidary saws are believed to have first appeared in China about 1900-1600 BC (Till and Swart 1986).
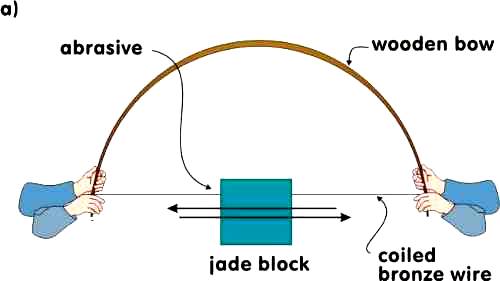
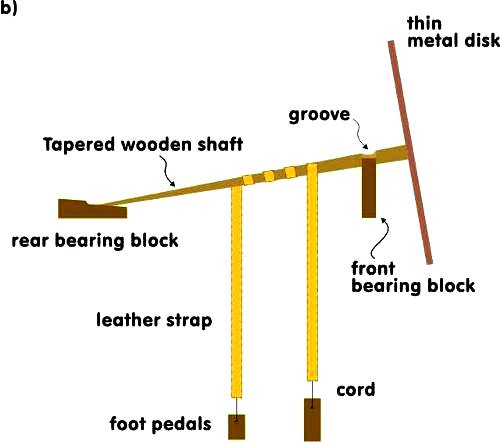
In the rock cutting experiment of Stocks (2001) the slabbing saw consisted of a 14.5 kg saw blade made of copper, which was 1.8 m long, 15 cm wide, and 6 mm in thickness. Two tests were conducted using quartz sand abrasive, one under dry and the other under wet conditions. In the case of the test using dry sand abrasive a saw with a flat-edged cutting surface was used, and a notched cutting surface was used in the case of the test using wet sand.
The granite block used by Stocks (2001) was quarried at Aswan. The surface of the block was initial pounded flat along the line of sawing. In the case of the test with dry sand abrasive, 2 boulders were attached to either end of the saw with ropes to act as weights (Fig. 7). The total weight of the saw was 45 kg, and this exerted a downward pressure of 1 kg/cm2on the cutting surface of the saw blade. During the wet sand test a wooden frame, attached to the top of the saw blade, was used as a weight.
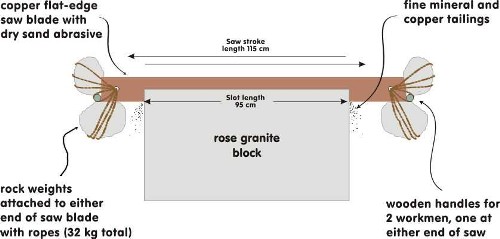
In both tests a team of 2 worker, one on either end of the saw, drew the saw back and forth across the granite surface. It was noted during both tests that the workers had some trouble keeping the saw blade perpendicular to the cut surface of the granite block. This produced a rocking of the saw blade from side to side as the blade was drawn back and forth. As a result, the slot cut in the granite exhibited a V-shaped cross-section (Fig. 8). Stocks (2001) gives for an example Djedefre’s granite sarcophagus (9th Dynasty) located in the Cairo Museum, which contains two partially sawn V-shaped slots similar in appearance to that produced in the modern slabbing test.
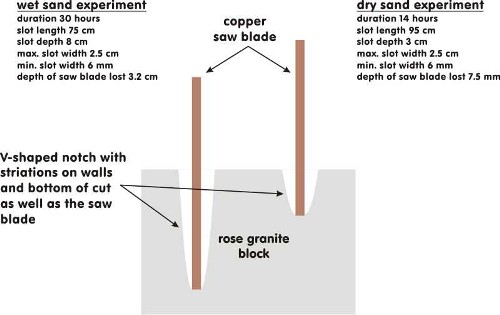
Although not mentioned by Stocks (2001), this type of V-shaped notch may be elevated to some degree by slates attached to the end of the block being cut. This is also used in modern slabbing saws and was described in a smaller scale lapidary saw by Theophilus in c.1100 AD (Fig. 9):
If you wish to cut crystal, fix four wooden pins on a bench, with the crystal lying firmly between them. These pins are so arranged that they are joined together in pairs, above and below, so closely that the saw can hardly be drawn between them and can nowhere be deflected. Insert the iron saw and, throwing on sharp sand mixed with water, have two stand by to draw it and to throw on the sand and water without stopping. This is continued until the crystal is cut into two parts (Naum 1962; page 170)
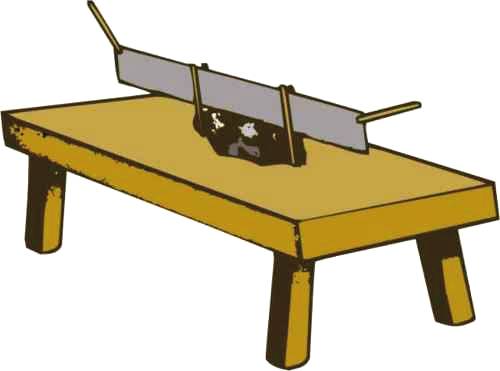
During the experiment striations of varying depths and widths were produced on the cut surface of the granite, which were rough-edged and parallel. These were presumably the result of angular quartz fragments embedded in the sides and bottom edge of the saw, which would have been drawing over the rock surface during the sawing process. Copper is soft enough that abrasive particles can be embedded into the metal, which is what makes this metal an ideal lapping material (Sinkankas 1984). The saw blade was noted by Stocks (2001) to have numerous pits on its sides and bottom. The cutting was observed to be easier in the case of dry abrasive than that of wet abrasive. In the wet test the wetness of the abrasive slurry needed to be monitored, since if it dried the sawing became more difficult. Both the dry powder abrasive and the abrasive slurry were added at either end of the cut slot during the cutting process. New abrasive was continually added to infuse the cutting surface with newer angular grains of quartz, since as cutting occurred the abrasive was reduced in grain size and the angular edges of the quartz grains were rounded off by abrasion making them less effective.
As sawing proceeded during the dry sand test the tailings, containing both copper and rock powder (consisting of both the granite and abrasive), were easily collected. In the wet test the tailings were washed away by the slurry. Stocks (1989; 1997) proposes that the tailings of the cutting process could be used in the manufacturing of a faience, from a water-based paste of calcite derived tailings (from limestone and travertine coring) and sodium bicarbonate (natron). As well, blue glazes can be produced from diorite and granite tailings. Both the blue glazes and the faience produced by Stocks resembles both chemically and in appearance those common to the ancient Egyptian’s. Stocks (1993) suggests that tailings could also be used as a polishing abrasive because of its 0.5-5 micron grain size, and also as an abrasive for the drilling of beads. A grain size of 5 microns (0.0002″) is ideal for lapping gloss finishes on rock surfaces, since the transition from frosted to semigloss lapidary finishes occurs with abrasives about 15 micron in diameter, and high quality lapidary polishes are generally done today with abrasive grain size of 6 (0.00025″) to 0.5 microns (0.00002″) (Craig & Vaughan 1981).
The rate of rock removal is similar for both the wet and dry sand tests at about 12 cm3/hour. Stocks (2001), after comparing the ratios of volume, weight, and depth of removal between the copper saw blade and the granite block (Fig. 8), concludes that the dry test with its flat-edged blade is distinctly better than that of the wet sand test with its notched blade. This is the result of the rate of degradation of the copper saw blade being greater in the wet tests, resulting in a more costly enterprise. As well, the tailing from dry cutting can be collected and used for other purposes. Because of the inexperience of the work teams in these modern experiments, it was suggested by Stocks (2001) that the rate of cutting could be increased by a factor of 2 with increased experience.
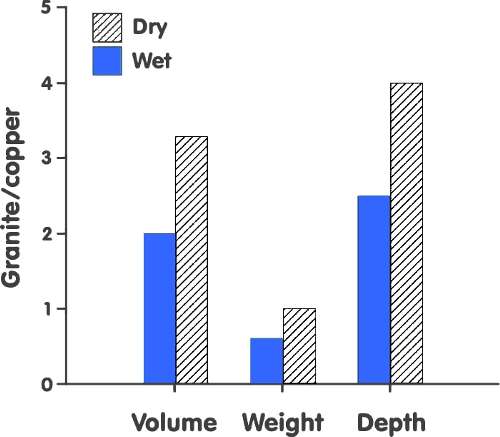
Fig. 10 Ratios of granite/copper lost during the slabbing saw experiment (after Stocks 2001). Stocks also conducted experiments on cutting limestone with copper lapidary tools. The rate of cutting limestone with a copper slabbing saw was 15 times greater than that observed in granite (Stocks 1999). The rate of copper loss would be expected to be very low due to the similarity in hardness between the mineral calcite and copper. This was demonstrated by coring drill experiments conducted by Stocks (1993), in which a ratio of length of copper tube lost from the drill bit to stone depth penetrated was less than 1:00. Copper lapidary saws would be very effective in the working of most limestones, since quartz abrasive is about 5 times harder than calcite.
These experiments demonstrate that the ancient Egyptians could have, using simple technology and the material available to them during their history, worked rocks with copper, bronze, and iron saws. It would be expected that for soft stones like limestone it was routinely used. In the case of hardrocks like granite, the expense incurred by the loss of copper during the cutting process (less with bronze and iron) would restricted it to royal monuments, for usage where other tools would not suffice (Arnold 1991).
a) Introduction
b) Copper slabbing saws
c) Copper coring drills
b) Stone vessel making
e) Bead making
f) Relief carving
g) Stone sculpture carving
h) Lapping and polishing
References
Arnold, D. (1991) Building in Egypt: pharaonic stone masonry. Oxford University Press, New York, 316 p.
Borchardt, L. (1905) Das Re-Heiligtum des Königs Ne-woser–Re’ (Rathures). Vol. I, Der Bau. Berlin.
Borchardt, L. (1907) Das grabdenkmal des königs Ne-user-re. J.C. Hinnrichs, Leipzig.
Clark, S. & Engelbach, R. (1930) Ancient Egyptian masonry. Oxford University Press, New York, 242 p.
Craig, J.R. & Vaughan, D.J. (1981) Ore microscopy and ore petrography. John Wiley & Sons, New York, 406 p.
Lauer, J-P. (1962) Histoire monumentale des pyramides d’ Égypte. Vol. 1, Les pyramides à degrés (IIIe Dynastie). BdE, no. 39, Cairo.
Long, F.W. (1976) The creative lapidary: materials, tools, techniques, design. Van Nostrand Reinhold, New York, 136 p.
Emery, W. (1972) Archaic Egypt. Penguin Books, Harmondsworth, 269 p.
Goneim, M.Z. (1956) The buried pyramid. Longmans, Green and Co, London, 155 p.
Lucas, A. & Harris, J.R. (1962) Ancient Egyptian materials and industries. E. Arnold, London, 523 p.
Naum, G. (1962) Of divers arts. Pantheon Books, New York, 205 p.
Petrie, W.M.F. (1883) The pyramids and temples of Gizeh. Field and Taer. London, 250 p. (e-book link)
Petrie, W.M.F. (1974) Tools and weapons. Aris & Phillips, Warminster, UK, 71 p.
Reisner, G.A. (1931) Mycerinus, the temples of the third pyramid at Giza. Harvard University Press, Cambridge (MA).
Ruffle, J. (1977) Heritage of the pharaohs: an introduction to Egyptian archaeology. Phaidon, Oxford, 224 p.
Sinkankas, J. (1984) Gem cutting: a lapidary’s manual. Van Nostrand Reinhold, New York, 365 p.
Stocks, D.A. (1988) Industrial technology at Kahun and Gurob: experimental manufacture and test of replica and reconstructed tools with indicated uses and effects upon artifact production. Unpublished Master’s thesis, University of Manchester.
Stocks, D.A. (1989) Ancient factory mass-production techniques: indications of large-scale stone bead manufacture during the Egyptian New Kingdom Period. Antiquity, 63, 526-31.
Stocks, D.A. (1993) Making Stone vessels in Ancient Mesopotamia and Egypt. Antiquity, 67, 596-603.
Stocks, D.A. (1997) Derivation of ancient Egyptian faience core and glaze materials, Antiquity, 71, 179-82.
Stocks, D.A. (1999) Stone sarcophagus manufacture in ancient Egypt. Antiquity, 73, 918-22.
Stocks, D.A. (2001) Testing ancient Egyptian granite-working methods in Aswan. Upper Egypt, Antiquity, 75, 89-94.
Till, B. & Swart, P. (1986) Chinese Jade Stone for the emperors. Art Gallery of Greater Victoria, Victoria, B.C, 144 p.
Wainwright J. (1971) Discovery of Lapidary Work. Mills & Boon, London, 216 p.
Zuber, A. (1956) Techniques du travail des pierres dures dans l’Ancienne Égypte. Techniques et Civilisations, 30, 196-215.
Links
Ancient Egyptian Furniture and Woodworking by Geoffrey Killen, with embedded photographs by Lorraine March-Killen.
Ancient Egyptian Stone Technology
The Egypt Archive – Jon Bodsworth’s image archive of ancient Egyptian antiquities